Even on a warm Friday afternoon, the floor stammers with activity at Raytec’s garment factory in the west of the Cambodian capital of Phnom Penh.
Some of the final products made here are stamped with logos for small-town organisations in the US heartland; others are limited-edition items for household name brands such as eyewear designer Oakley.
But not everything needs a human eye or hand, factory manager Kim van der Weerd said, nodding at a nearby computer screen.
“This used to be somebody’s job,” she said.
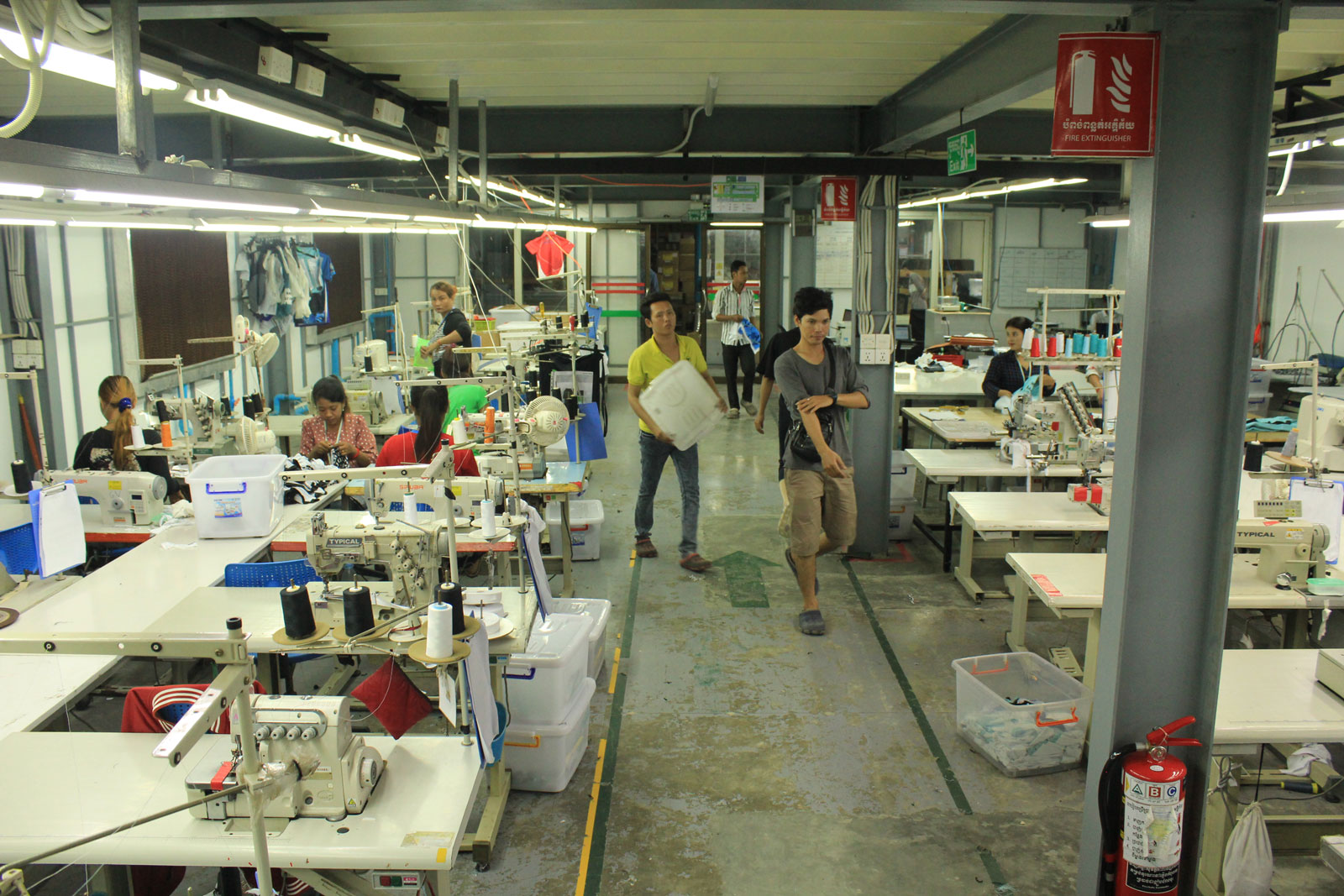
As she spoke, a graphic designer double-checked a virtual layout of garment panels arranged like puzzle pieces on what would eventually be a real-life scroll of paper.
While it gets approved by human staff before going to print, the arrangement was made entirely by a computer programme tasked with laying out as many panels as possible on a piece of material, maximising the number of eventual cut-outs while reducing waste.
Now, thanks to the help of programmes like this one used widely in the industry, the work of the arranger has been completely automated – though things still look a little more traditional in other rooms of the factory.
Sewers perch before their machines as fabric blurs between hand and needle while another group of workers sorts items by hand into individual orders, counting out whimsically patterned covers for high-end ski goggles and setting them aside for shipping. Elsewhere, staff stitch together apparel for Cambodia-based garment manufacturer Pactics – custom-printed goods for clients ranging from local sports teams to international brands selling athleisure goods such as leggings and lightweight tops.
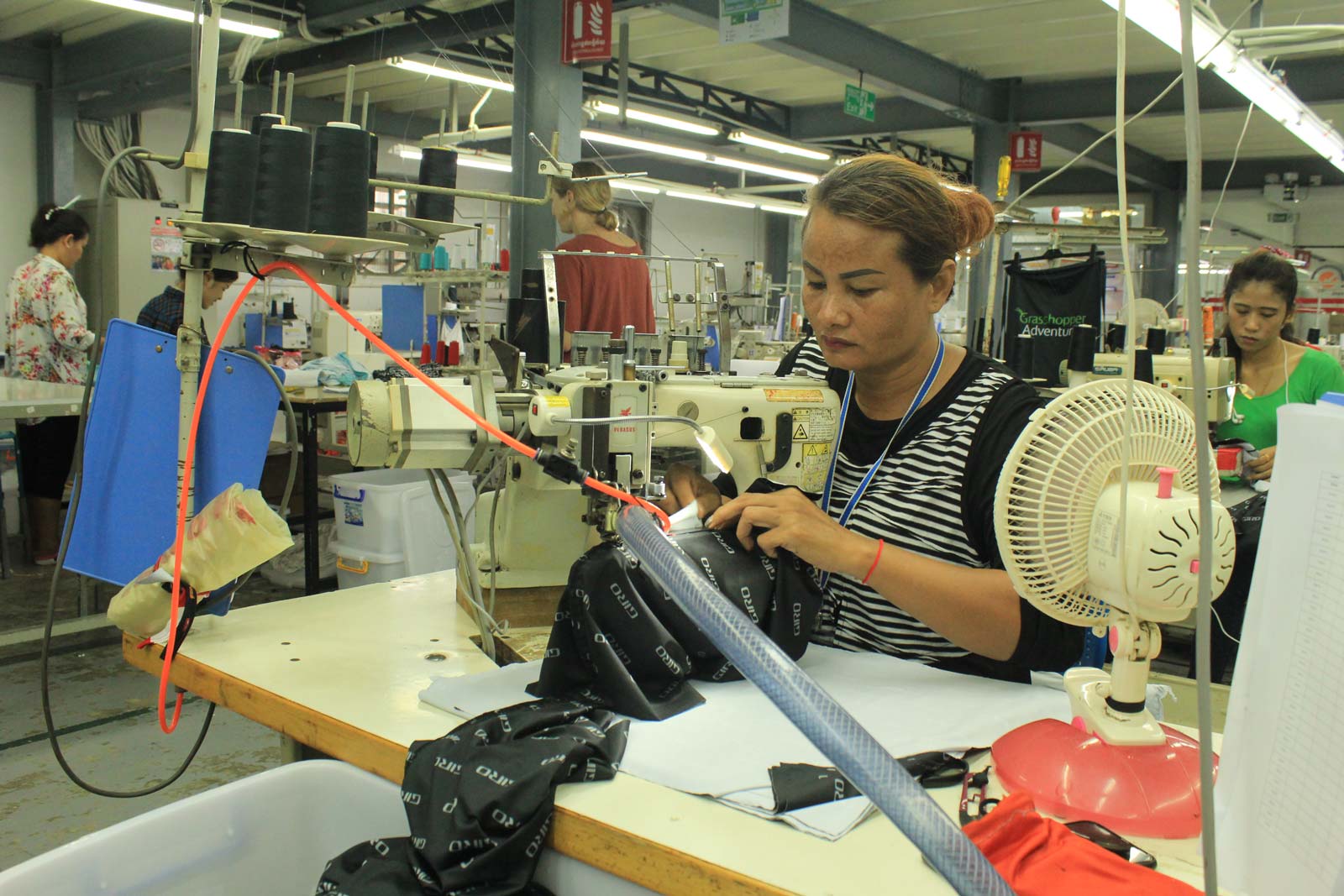
This kind of scene could be the future for the apparel sector, which in recent decades has forged a long supply chain linking low-wage producers, mostly in Asia, with higher-income consumers in Europe, Japan and North America.
But major apparel companies could soon have another option coming online. That potential difference-maker revolves entirely around automation, a process that replaces human labour with that of a machine. For the garment industry, a fully robotic manufacturing line could in theory work relentlessly spinning out clothing for as long as the power stays on.
They’re not much for personality, but robots never go on strike. Nor do they protest wages or working conditions or demand workers’ rights – the type of street action that has helped push Cambodia’s government into repeated local minimum wage hikes in recent years.
There are about 100 workers total at the Raytec factory doing everything from sewing to security. Busy as they are, they’re but a fragment of the workforce of approximately 800,000 people stitching up the Kingdom’s growing apparel sector. An International Labour Organization (ILO) report published in August stated the textiles, clothing and footwear (TCF) sector exports marked $6.3 billion and accounted for 78 percent of Cambodia’s total merchandise exports in 2015.
Across Asia, the ILO wrote, the TCF sector employs upwards of 40 million people making about $601 billion in exported goods.
But the rise of automation is leading many to question whether most of these jobs will even exist in a few years. And while automation is touted as bringing about an imminent revolution in manufacturing, it isn’t a new concept, with the earliest forays into machine production in the textile manufacturing that marked the early days of the Industrial Revolution in the United Kingdom. Robot-assisted manufacturing has only grown since then and has come to form a pillar of modern productivity, perhaps most visibly in the automotive industry.
Delegating tasks to machines is a go-to solution in work that is simplistic and repetitive. In some ways, it would seem to be a good fit for apparel production, which is usually made up of series of atomised tasks that by themselves are relatively easy to accomplish.
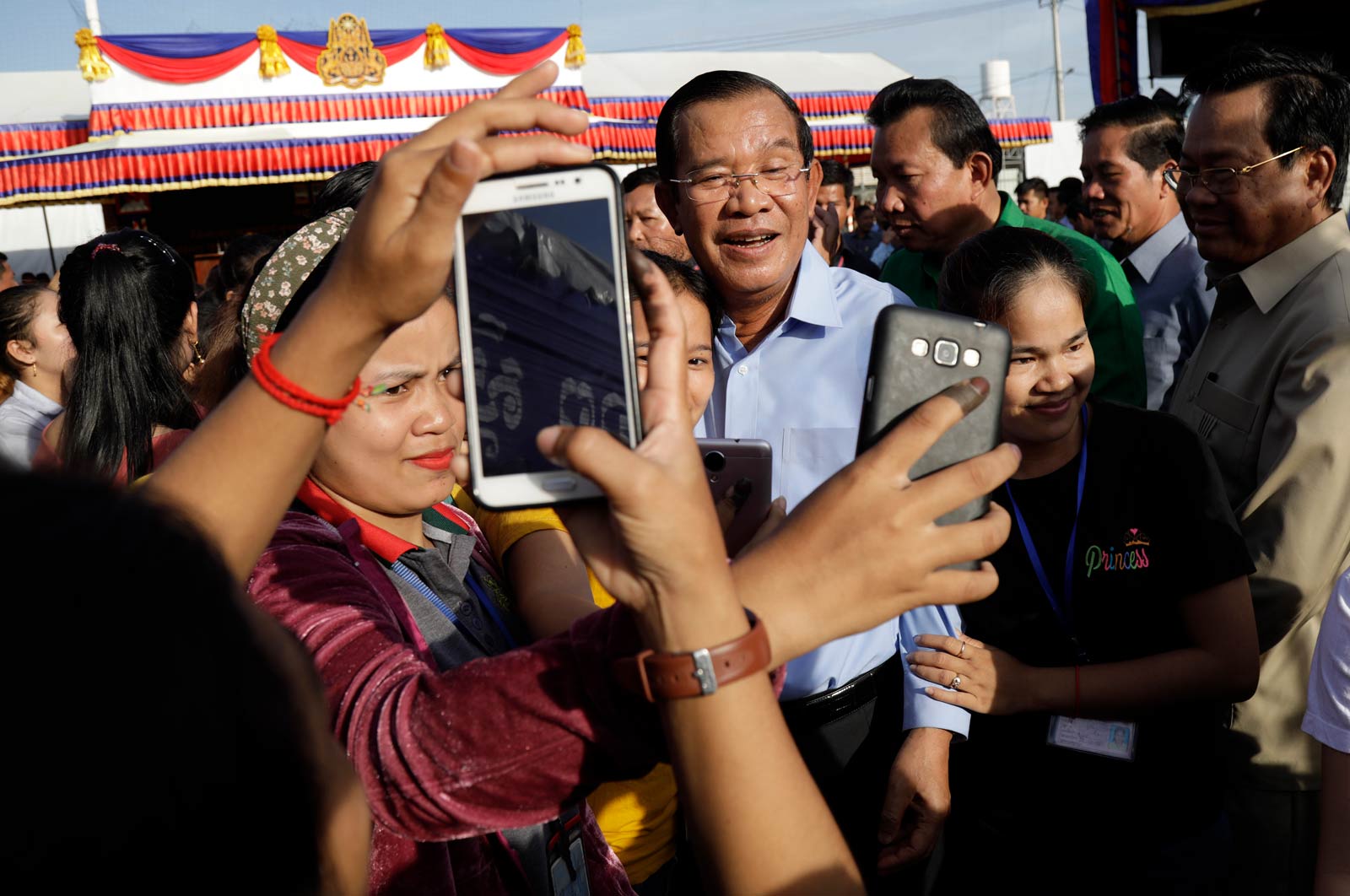
However, despite the hype about progress on the one hand and dire warnings of job losses on the other, automation has not yet emptied the factories of Asia.
It’s easy to take human aptitudes for granted, but the millions of dollars put into robotics research and development have yet to come up with anything to match the dexterity of a human hand.
Though garment workers are not typically trained to complete an article of clothing from scratch, they are more than able to run a piece of cloth through a sewing machine – a task that is usually beyond any robot seamstress.
Unlike the unyielding steel that robots can manipulate with ease in car factories, textiles are nearly fluid by comparison – bunching up, folding, wrinkling, creasing. While a human can note such anomalies on the fly and stretch and twist as needed, an automated system has trouble even seeing what’s happening in the first place, much less reacting in time to rescue the garment.
Despite these robotic fat fingers, Nate Herman, a senior vice president of supply chain at the American Apparel and Footwear Association, said the push to automate the garment manufacturing process has been ongoing for about the last 15 years.
“There are a number of strivers in the market for that,” said Herman, discussing automation technology.
“Building machinery where people no longer do the work – in apparel, it’s been very difficult to do that successfully and in a consistent manner”
Nate Herman, senior vice president of supply chain at the American Apparel and Footwear Association
Automation’s chief allure is its potential to simplify and cut costs in the garment industry, which has, like many other manufacturing sectors, spawned complex transnational supply chains.
Take, for instance, the cost outlook for China, where Western producers flocked in the 1990s to take advantage of a liberalising economy and cheap labour.
Years later, rapid economic development and subsequent wage increases mean that the picture is much less clear than it once was, with producers having shifted some of operations in the intervening year to China’s Southeast Asian neighbours, where wages too are now starting to edge up.
China, the largest destination for offshore production, has rapidly developed into a consumer nation, with hundreds of millions of people lifted into the middle class and with steady technological advances seeing it emerge as a global leader in some high-tech sectors.
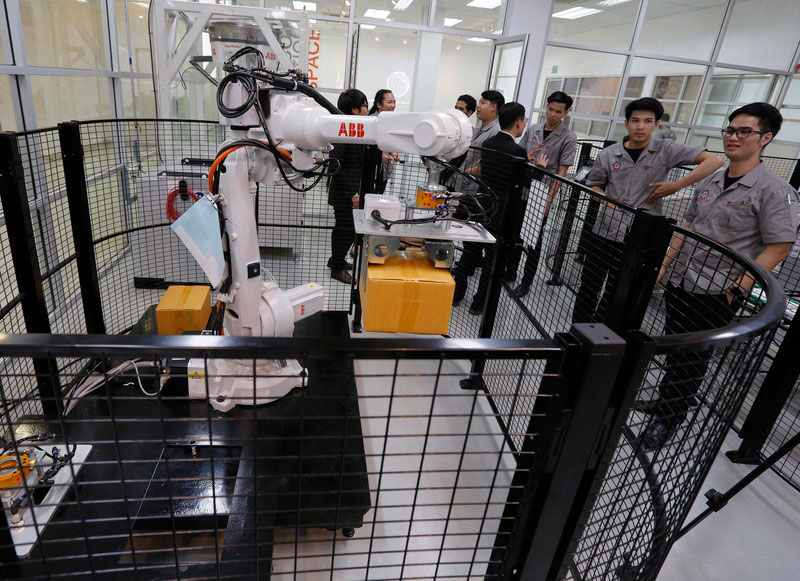
That rise has in part spurred the US-China “trade war,” which has in turn accelerated the drift of manufacturers, who once made their home-away-from-home in Chinese factory cities, to elsewhere in the region. While that has prompted economic windfall for Southeast Asia in the last decade or so, the development of tech-assisted production lines are already closing the price gap between East and West and could see those recently acquired Southeast Asian jobs shift once again.
In response to that, consulting firm McKinsey and Co. notes in the 2019 edition of its State of Fashion report that 60% of apparel procurement executives surveyed expect their companies will be sourcing more than one-fifth of their total volume from “nearshore” sources by 2025, sending manufacturing back to the lower-cost markets adjacent to some of the world’s wealthiest countries.
That’s a lot of goods made closer to home, but they’re still not coming all the way back – at least not yet. McKinsey’s 2019 outlook stated the labour-cost-gap between these nearshore and offshore zones is shrinking, or even “disappeared” in places such as Turkey and Mexico – the original cheap labour zones for Europe and the US.
While the economics build one case for greater automation, discerning or fickle consumers make another.
Shoppers are increasingly looking for what’s become known as “fast fashion” and more customisable pieces, choices that often go out in smaller batches and require shorter lead times from design to production to shipping. Making these kinds of garments can be beyond the scope of factories that focus on mass production of lower-value goods, and higher-value producers with better proximity to market tend to save valuable transportation time.
These sales have been abetted by online shopping and the harnessing of so-called “big data,” which together enable manufacturers to track products in so-called “real-time” and better understand customer preferences.
This tantalising vision of seemingly infallible efficiency has seen automation cast into a sort of holy grail for garment manufacturers. But much like that fabled cup, the seamless all-robotic factory remains out of reach for now.
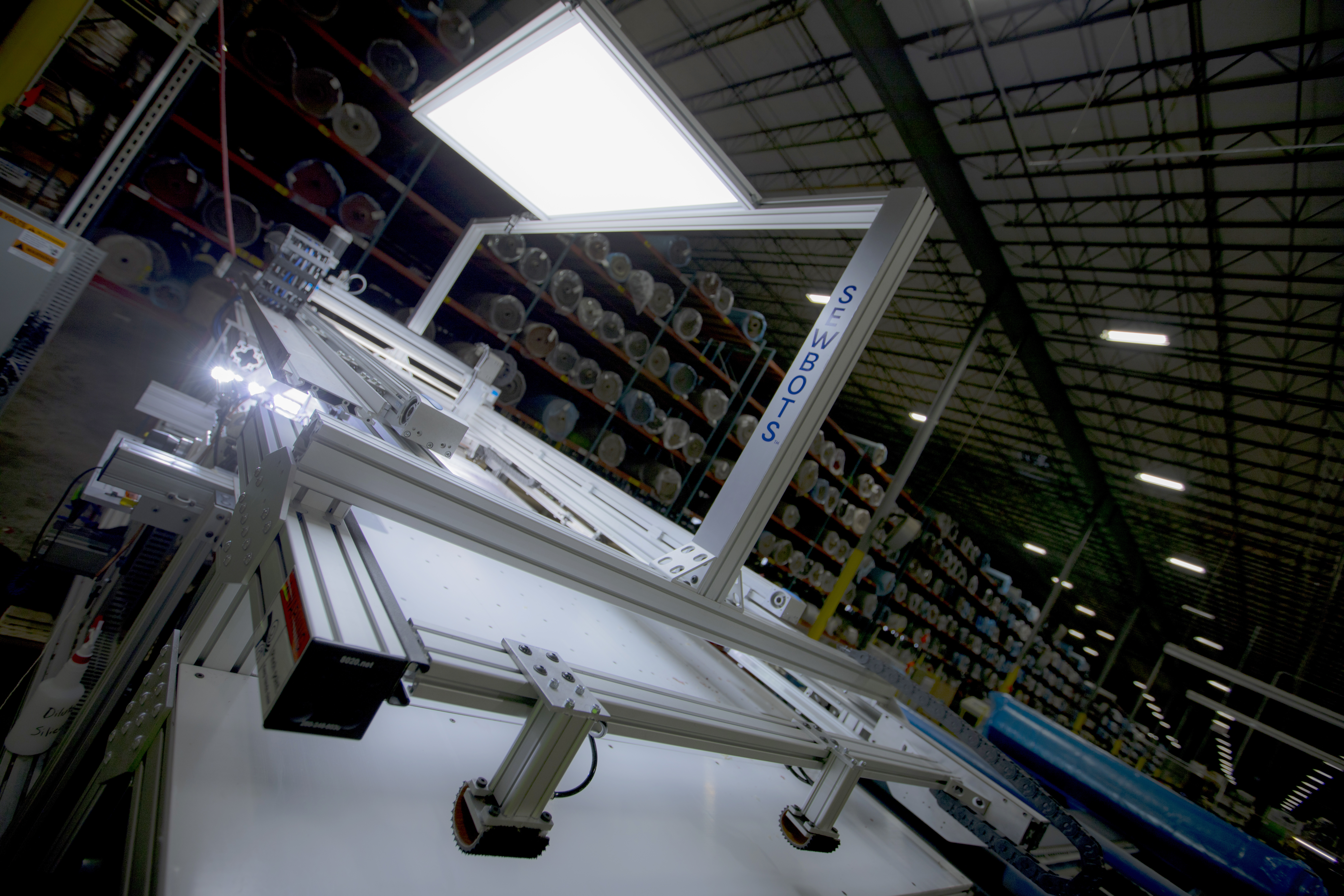
Herman didn’t want to speculate too much on the timeframe for that kind of automation, though he still threw some cold water on the claims of an imminent phase-out of human workers.
“Building machinery where people no longer do the work – in apparel, it’s been very difficult to do that successfully and in a consistent manner,” he said. “There are important innovations in reducing development and production time on the margins, but it hasn’t gotten to the fundamental issue.”
His assessment? “I think we’re a number of years away from where we could fully automate.”
Industry experts in Cambodia have struck a similar note when communicating to domestic audiences. Speaking at a business panel event last summer, John Cha of the Garment Manufacturers Association of Cambodia said that automation has not drained the local workforce. Cha dismissed the notion of automated production being some harbinger of doom for local apparel and said new technology has become a vital part of production.
“We have more orders. We need more workers. And we are more automated now compared to 20 years ago when everything was manual. Automation did not remove workers,” local media quoted Cha as saying. “There are various levels of adaptation [to digital industry]. Some [factories] are at the very initial stages. Some are very advanced.”
Cha’s words may be a balm to the techno-anxious in the region’s apparel factories, but others have continued sounding an alarm about job impacts possibly barreling down the pipeline. A 2016 report on the Southeast Asian garment industry by the ILO declared “significant shares of garment workers in Asia are indeed at high risk of automation” and identified some 88 percent of the Cambodian labour pool as in that danger zone. The report said the same for 64% of garment workers in Indonesia and 86% in Vietnam.
“In the long-term, I think the new technologies coming to [the textiles and garment industries] are going to create different and better jobs”
Devin Cook, executive producer of the MIT Inclusive Innovation Challenge
The ILO report concluded that “Bangladesh, Cambodia, Indonesia, Myanmar and Vietnam will need to rigorously follow China’s movements in using technologies to maintain competitiveness and move up the value chain and continually evaluate how the region should use garment as vehicle for growth.”
That’s the idea, anyway, but tech developers around the world are also doing their best to speed that pace as much as humanly – or robotically – possible. US robotics firm SoftWear Automation has developed a line of machines dubbed “Sewbots” that can already produce simple products such as bath-mats without human help. The company claims its development timeline will have its robots producing crew-neck t-shirts within a year and more complex garments like jeans within the next four years.
Sports apparel giant Adidas has already opened AI-heavy factories in Germany and the US, a brand of facility known by the very utilitarian title of SpeedFactory. The shoe production centres in the respective states of Bavaria and Georgia are showcases of the company’s investment in autonomous technologies such as 3D printing and computerised knitting. They could soon have the capacity to produce a combined 1 million pairs of shoes each year – an impressive feat, though still only about a day’s worth of Adidas suppliers’ total annual output of roughly 360 million pairs of branded sneakers.
One of those suppliers might just show them the way to bigger, better robot-powered production. Chinese firm Suzhou Tian Yuan Garments Co., or TY Garments, is one of Adidas’ largest producers of shirts and other apparel. Last year, TY Garments opened a factory in the US state of Arkansas, employing hundreds of human workers from a historic textile production region. The American South, once home to an infamous slave trade that worked a booming cotton industry, was a textile powerhouse through the early 20th century and provided more than 1.3 million jobs at its peak in 1948.
Thanks to new technology, textile production in the South is on the rise once again. The future labour needs in garments there are a little less clear though, as TY has a stated goal of developing the world’s first full-auto T-shirt production line staffed entirely by Sewbots. SoftWear plans to install the Sewbots at the Arkansas factory midway through next year.
Company chair Tang Xinhong has previously told media outlets in the fashion sector that he plans to invest in 21 digital-only production lines with capacity to spin out one shirt every 22 seconds for a daily total of about 800,000 garments.
“Around the world, even the cheapest labour market can’t compete with us,” he told Just-Style magazine this past June.
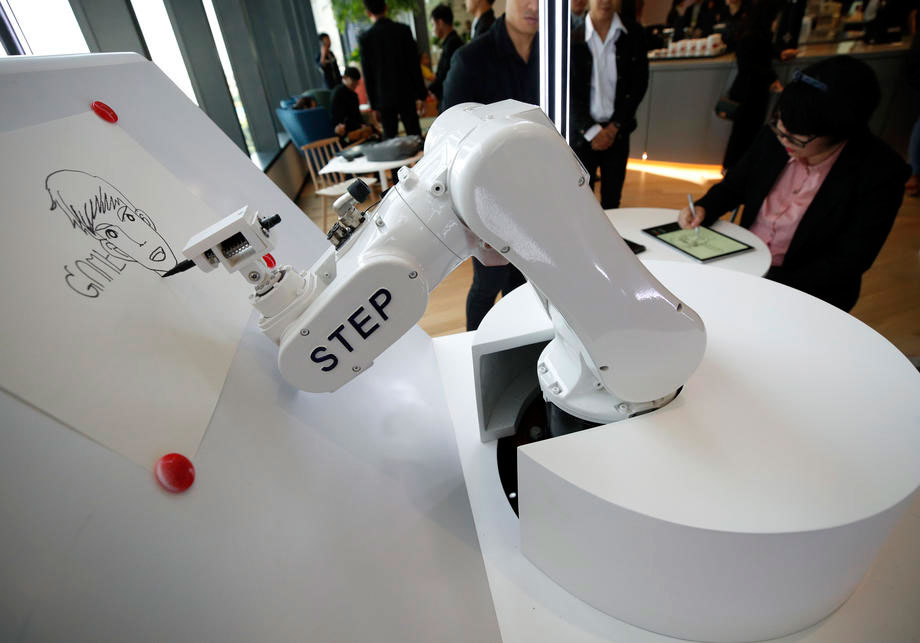
Critics of the push for an increasingly robotised economy say that automation will displace millions of human workers around the world. This will happen eventually, most analysts agree, but there are caveats, while predictions of near-term job losses vary wildly.
UK-based Oxford Economics estimates that by 2030 robots could replace human labourers in about 20 million jobs, while McKinsey projects anything from 75-375 million workers displaced by automation within the same period. What the statistics lack in specifics they make up for in their ability to grab headlines, but exact numbers aside, technologists agree that change is coming to the global workforce.
“I think the reality is some jobs are definitely going away,” said Devin Cook, executive producer of the MIT Inclusive Innovation Challenge. “We can’t turn away from that fact and pretend everything with technology is going to be rosy in the short-term.”
Cook’s office at MIT is an international, future-focused extension of the university’s business school that awards grants to entrepreneurs who use digital innovation to meet community needs, both economic and social.
“When you’re talking about price differences that are so, so small, when you’re talking about a matter of cents, all of this matters. It makes the difference between getting the order and not getting the order.”
Raytec’s factory manager Kim van der Weerd
Recipients of past awards have been involved in fields as diverse as childcare, microlending and work-on-demand apps. As the name suggests, the initiative tends to focus on tech concepts that are broadly accessible. The messaging gets to the anxieties of many who fear that devalued human labour could create a world rife with new avenues for exploitation by those who own automated capital.
But if Cook’s assessment sounds optimistic in the light of potential human obsolescence, it’s also backed by history.
“We’ve seen this time and time again,” she said, pointing to the initial turmoil caused by the Industrial Revolution. “There was a lot of difficulty and pain, but in the longer term people who made it through that transition were able to work shorter hours and got benefits from their employers.
“In the long-term,” she said, “I think the new technologies coming to [the textiles and garment industries] are going to create different and better jobs.”
Cook sees it as the responsibility of the technologist to “speed that transition so the fewest people possible are suffering,” and her counterparts in the field usually point to retraining as a major way to avoid the potential downsides of the process.
More and better training would surely help, but it remains to be seen how humans will adapt to a growing and increasingly-capable robotic workforce.
It’s also unclear how much interest and ability a country like Cambodia – where economic disparity is high and public services are sparse – has in preparing its people for a new economic reality.

Cambodian workers in a garment factory in Phnom Penh Photo: Mak Remissa / EPA
For garment makers today, that reality is already something to be reckoned with.
Though her factory in Phnom Penh is a good example of the contemporary mix of human and machine labour, Van der Weerd said the siren call of automation echoes to anyone in the apparel industry, where margins are tight and producers are pushed by brands to cut costs.
“When you’re talking about price differences that are so, so small, when you’re talking about a matter of cents, all of this matters,” she said. “It makes the difference between getting the order and not getting the order.”