Belgian-born bicycle designer and founder of Mekong Creations Bernard Kervyn isn’t afraid to put his “unbreakable” bamboo to the test: “Take a piece of 20mm gauge bamboo, drill it with 10mm holes every centimetre, place the bamboo between two concrete blocks and invite two people to dance on it. It will bend, perhaps split but never break.”
It’s this structural “softness” that gives bamboo the edge over its high-tech, highly rigid rival, carbon fibre. “When you ride on bumpy roads, the bamboo absorbs vibrations – it’s a natural shock absorber,” says Bernard.
Bamboo’s secret lies in its woody fibre: microscopic tubes in the stem give the plant its strength, which is comparable to light steel, while considerably heavier than carbon fibre. The frames average three kilograms, but the synthetic epoxy resin joins account for much of the total. Bernard’s company then wraps the joins in hemp grown in northern Vietnam to keep the design aesthetic. “They are really striking, beautiful objects,” Bernard says.
Part of the grass family, bamboo is one of the fastest-growing plants on Earth, with some of its 1,400 species able to shoot up almost one metre in 24 hours. Bamboo has been touted as one of the most sustainable and environmentally friendly crops, in part due to its proliferation, plus its ability to sequester C02 and reverse soil degradation, which make it a good candidate for reforestation efforts.
The tamvong species, which translates to “steel” in English, is used for building bicycles, but it’s not strong enough until it’s at least 3 years old, according to Bernard. The synthetic resin in Bernard’s bicycles may not align with the green credentials of the bamboo which it holds together, but it does make repairing frames easier: “Even when a frame has split ten or 20 centimetres long,” Bernard explains, “you just need a little bit of resin or glue in the split, and that’s it.”
History of bamboo bicycles
Globally, there are over a dozen organisations making bamboo bicycles today, but their legacy extends back much further: the first patent was taken out by British Bamboo Cycle Company in 1894. Its unveiling at the London Stanley Show caused a sensation, but the effect on the bicycle-riding public was not lasting.
Bamboo bicycles didn’t hit production lines again until over a century later, led by American professional frame builder extraordinaire Craig Calfee. Calfee was the brains behind the first carbon fibre frames to enter the Tour de France, which he correctly predicted would one day constitute 100% of bicycles in the race.
While watching his dog play with a bamboo stick in the mid-1990s Calfee was struck by the reed’s strength. Still buoyed by the success of carbon fibre cycles racing in the Tour de France, he built a prototype bamboo bike as a gimmick for a trade show. It wasn’t until 2005 that Calfee’s first-class bamboo frames hit the road to great fanfare, inspiring Bernard and others to go into production.
“There’s nothing revolutionary about making bikes out of bamboo,” Bernard notes. “Although, of course, the techniques have evolved over time.”
Nowadays, demand for bamboo bicycles is increasing, with a number of purveyors in recent years even offering people the chance to learn how to build their own frames.
Like Calfee, Bernard does not foresee bamboo displacing carbon fibre bicycles in the Tour de France. They are occasionally seen in races in the US however, such as the 2014 Red Hook Criterium held in New York where a custom bamboo build was the first over the finish line.
“Sure, they are heavier than carbon fibre bikes,” says Bernard “but for off-road riding they’re ideal.”
6 steps to make a bamboo bicycle
- Source your bamboo – ideally tamvong species, at least 38mm thick and 3 years’ maturity
- Soak the bamboo in a solution of boric acid for a few days to treat the bamboo
- Leave the bamboo to dry in the sun for up to 1 week
- Cut your bamboo to size for your frame
- Prepare materials for your joins: soak hemp fibres in a solution of epoxy resin for durability
- 50 hours of workmanship go into every frame, with half a day for assembly
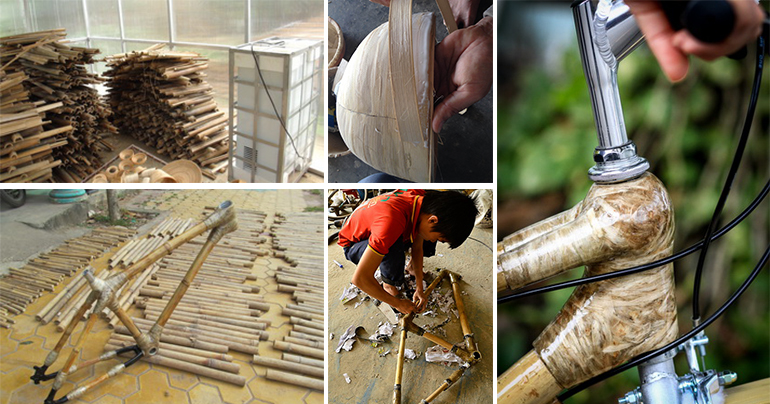
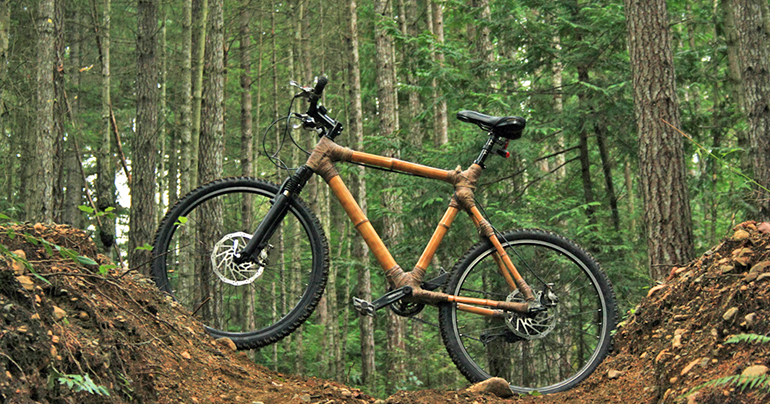